Studying The Properties of Mortar Produced Using Juss as a Partial Substitute for Cement
2024-03-27 | volume 2 Issue 1 - Volume 2 | Research Articles | Fatima Alsaleh | Feras Al adday | Abed Alhakeem BanoodAbstract
Recently, many enterprising attempts have been made to create more sustainable cement mortar mixes using modern technologies. Modified mixtures are a promising part of green infrastructure, which contributes to reducing environmental impact and cost. Determining the properties of modified cement mortar using Al Juss binder (JB) is the focus of this study. JB is a locally made binder from heated white stone (gypsum stone) near the Deir Ezzor region, Syria. The cement, which is the main element in the cement mortar, is replaced with different JB ratios of 0%, 10%, 25%, 50 and 75% of total cement weight. The results revealed that the compressive strength at 28 days of age of 10% JB-mortar was 26.5 MPa, matches type M-mortar (20 MPa), and 25% JB can be used in type S-mortar. As a result, it has been confirmed that cement-JB mixture mortars containing 10% or 25% of JB do not meet the properties achieved by control cement mortars. However, they possess acceptable properties such as compressive and flexural strength, initial and final setting time, and expansion value of the cement.
Keywords : Al Juss Binder, Portland Cement, Juss-Cement Mortar, Mechanical Properties.
INTRODUCTION
Substitutes to cement are a sustainable way to decrease the overuse of cementitious materials, and it is gradually becoming important to include them in the building sector [1]. Energy consumption is the major environmental concern associated with cement manufacture, including the direct use of fuel to extract and transport the raw materials as well as the high energy required for calcination, which is provided by burning of coal, coke, natural gas, diesel and fuel. Cement manufacture consumes about 1758 kWh per ton of cement. Mortar is one of the decorative building elements in addition to its role as a binder for the block and is widely used in the construction field. The mortar mixture consists of Portland cement, fine aggregate, and water. Many adjustments have been made to the mortar concerning its components [2]. The various construction processes are one of the main sources of high carbon emissions, as the cement industry is a significant component in increasing carbon emissions. Using other cementitious materials to produce cement-based materials is an important technique to decrease carbon emissions, where the cement industry generates nearly 8% of global CO2 [1]. Fly ash and Silica fume (pozzolanic materials) are widely used as cement alternatives to produce cement-based materials [1]. The consumption of local raw resources is one of the obstacles to cement manufacture [3] [4]. In addition, issues related to climate change have attracted significant attention. However, more recently, issues related to local health aspects have been mentioned. Therefore, designers of building material mixtures seek to introduce sustainable technologies to reduce environmental impact [5] [6]. Current technological advances aim to improve the construction process in terms of speed, performance and financial productivity. The use of gypsum mixes that do not require high levels of heat during the production process is common [7]. Gypsum is a construction material known for its good performance against variations in humidity and its rapid ability to change shape and harden. However, gypsum materials have some disadvantages for use in construction, such as: not being hard or brittle, poor waterproofing and decomposing quickly. For this reason, many researchers have conducted numerous tests to determine and improve the performance of these materials. Archaeologists dated the earliest uses of gypsum about 7000 BC [8]. Many researchers aimed to replace raw building materials with wastes and biomass (low energy consumption binders) to increase the environmental efficiency of construction. Gypsum is considered one of these low-cost materials, that seems to be a suitable option for new constructions, in addition to being widely used in many restoration and rehabilitation operations for old buildings. The advantage in which gypsum is distinguished from cement and lime is its production at about 120-180 °C, with a much lower burning temperature and energy, while cement needs about 1500°C and lime needs about 900°C. Thus, the associated low energy makes gypsum a sustainable solution [9]. Concerning energy saving in buildings in European countries, around 75% of buildings need incomplete or complete repair because they are not energy efficient. Enhancing the performance of wall cladding (interior and exterior) is an important energy-saving technology as part of the rehabilitation and maintenance of damaged and older buildings [10]. As for Syria, this percentage increases very significantly as a result of the war that the country was exposed to, according to the observations of the authors themselves, to more than 90%. By the way, statistical reports issued by the International Energy Agency indicate that worldwide energy depletion in the building sector will reach 30% in 2060 if the existing ratio of increasing growth remains as it is now [11]. Accomplishing high energy efficiency in structures is the most demanding concern of governments internationally, which would cause a decrease in energy depletion and environmental problems related to CO2 emissions [11]. Various research projects and investigations began years ago to find suitable alternatives to reduce the concentration of carbon dioxide in the atmosphere, in addition to reducing the cost of building materials [12][13][14]. Unpredicted environmental hazards of carbon emissions resulting from cement manufacturing required for all structures in addition to depletion of raw resources are the most persistent tasks of future engineering. However, achieving sustainability by introducing natural materials that are affordable for various construction process is one of the preferable solutions. Due to the lack of searches done on JB, and its wide spread in the Deir ezzor region, it was necessary to draw attention to that product and define its specification. The key objective of this investigation is to determine the engineering properties of JB-based mortar. JB is used as a partial replacement of cement with varying ratios of 0%, 10%, 25%, 50% and 75% of the total cement weight. Then, comparative results between the cement mortars and JB-based mortar will be presented.
MATERIALS AND METHODS
JB: The southern region of Deir ezzor is generally famous as the extraction deposits of the raw material for the production of JB. A large number of limestone mountains, the most important of which are the southern mountains near the Qabr al-Wali area, the Hawooz area, the Tharda Mountains, and the ancient al-Jura area. A single limestone mountain mass is called a Maqtaa, it is a huge rocky mass that has a vertical cliff surface called a Gall. The chemical composition of JB was measured to determine its components (CaO, SO3, and H2O). Table 1 represents these compositions.
The different compositions of compounds are due to the heating process, which leads to the release of water and thus the restructuring of other molecules. After the trailer carries the load of stones to Namura, which is the main factory of the white JB, the workers collect the stones brought from the nearby mountain. Then the second phase begins when the workers, who are spaced about 2 meters apart, break these stones into sizes smaller than egg size, and then carry them manually to the dome of Al-Namoura, where they are distributed over its surface after being sieved so that the stones smaller than 2 cm in diameter are eliminated. After paving the dome with small stones, the third phase begins including the burning process, which lasts for two days. The purpose of the burning process is to separate the desert dust and impurities from the stones in addition to modifying the structure of the stones so that they become fragile and completely free of moisture. After one cooling day, the burned stones are taken to a stone grinder to be smashed into powder. The JB is manufactured from CaSO4⋅2H2O (gypsum), which is obtained from the mineral rock. Upon heating at a temperature of around 160°C, the gypsum converts to CaSO4.0.5H2O (JB) [16].
Experimental program
This section compares the performance of the cement mortar (0% of JB) with the cement-JB mixture mortar with different ratios of JB. Different specimens of mortar were prepared using the materials indicated in Table 2. The weight, volume and bulk density of cement, sand and JB are determined.
The proportions of the mortar components were as follows:
- The ratio of C/S (cement/sand) was 1:3, ISO 679: 2009 recommendation. These values must be expressed in terms of weight.
- A designed ratio of W/C (water/cement) was 0.5, Recommended according to ISO679:2009.
- The number of cubic specimens, 45, was used to measure the compressive strength of the specimens with dimensions of 5 x 5 x 5 cm, according to ASTM C109/C109M-20.
- And forty-five prismatic specimens were used to measure flexural strength. The specimens had dimensions of 4 x 4 x 16 cm, according to ASTM C109.
- Bulk density was determined using fifteen cubic samples, each measuring 5 x 5 x 5 cm.
- A total of 15 cubic samples with dimensions of 5 x 5 x 5 cm were used to measure the rate of water absorption.
Cement, water and JB were mixed in a mixer for one minute before sand was added. The total mixing time is about 3 minutes to get good adhesion between the cement, Al Juss, sand and water. The cement used is local ordinary Portland cement (grade: 32.5, specific gravity: 3.15, finesse: 3360 cm2/gr, chemical composition: shown in Table 3), and the water used is safe to drink. As for sand the Table, 4 represents some specifications of the crushed limestone sand used. To accomplish the comparison, five mortar mixtures were prepared that differ from each other in the percentage of cement and Al Juss, while the control sample was produced using pure cement as a binder and four samples that include JB with different proportions 10%, 25%, 50%, and 75% of total cement weight.
RESULTS
The properties of the modified cement mortar were evaluated using JB binder. The compressive and other properties revealed lower values compared to the cement mortar. The following is a presentation of the results conducted during the study.
The finesse of Cement (Blaine value) vs. JB replacement
The relationship between the fineness of cement and the JB mixture with the used JB replacement ratios is shown in Figure 1.
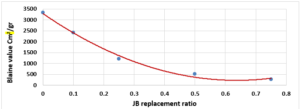
The fineness of the mixture decreases as the JB replacement ratios increase as shown in (Figure 1). The mixture’s fineness affects the workability, durability, strength, and hydration rate. This decrease is due to the increase in JB related to cement because it is finer than JB which was produced manually.
properties of fresh paste and mortar:
Study of Initial and Final Setting Times of Cement-JB vs. JB Replacement:
Figure 2 illustrates the relationship between the initial setting time and final setting time (measured according to ASTM C-191) of the mixture of cement-JB pastes with the JB replacement ratios.
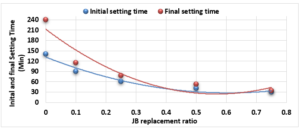
In the analysis of Figure 2, it can be noted how the initial and final setting times of the cement-JB mixture pastes decreased by increasing JB replacement ratios. At the 50% and 75% JB of the mixture, the initial and final setting times are close to each other. The decrease in both initial and final setting times of mixtures is due to the increase in JB, which causes them to lose their elasticity and become sufficiently rigid.
Study of Expansion of Cement-JB vs. JB Replacement according to Le Chatelier:
The expansion value of the cement and JB pastes versus JB replacement according to Le Chatelier is shown in Figure 3. The expansion value of the cement-JB mixture mortars increased by the increasing of JB ratios as shown in Figure 3. All of JB ratios do not show any significant expansion values. This increase is due to the fact that JB has a larger percentage of pore voids and is less homogeneous than cement, which was produced manually, and therefore has greater expansion values.
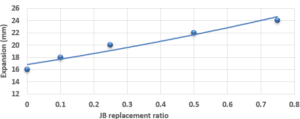
Study of Water Absorption value:
Figure 4 characterizes the water absorption value of cement-JB mixture mortars versus JB replacement, as the increase in the percentage of JB increases the water absorption value. JB is hydrophobic, as the increase in the percentage of JB increases water absorption value (In this case, I think that JB should be hydrophilic rather than hydrophobic). It can be clearly distinguished that all these values are less than 70%. Water absorption is the movement of liquid within unsaturated JB-cement samples’ pores under no external stress. JB, which possesses higher porosity, is known to have a more water absorption capacity, causing an increase in the absorption rate as JB content increases.
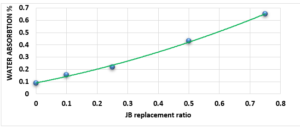
Properties of hardened mortar:
Compressive and Flexural Cement-JB Mortar Strength: Compressive and Flexural strength of the cement-JB mortar mixtures were determined at 2, 7, and 28 days of standard curing conditions (20 ± 2°C, and relative humidity >95 or immersed in water) as it is shown in Figures 5 and 6.
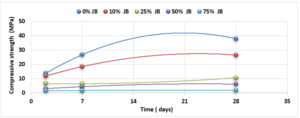
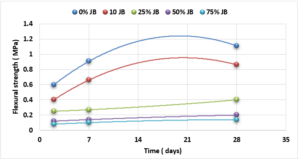
The values of compressive strength cement-JB mixture mortars are shown in Figure 5. The highest compressive strength can be clearly observed in the control samples (38 MPa), followed directly by mixtures containing 10% of JB (26.5 MPa), and then by 25% of JB (10.5 MPa). On the other hand, the lowest compressive strength of cement-JB mixture mortars was obtained at 75% of JB, reaching 1.9 MPa. Adding JB to cement causes an increase in the volume of the mortar, which leads to cracking of the bonds that connect the aggregates, thus reducing the compressive strength. The outcomes derived from the flexural strength tests are shown in Figure 6. This figure displays how the cement mixtures containing 10% of JB have higher flexural strength values than the other three JB ratios investigated (0.86 MPa). When JBs are added to cement, mortar volume expands, breaking bonds and reducing flexural strength.
Study the change of dry density according to the JB replacement ratios: The dry density of the cement-JB mixture mortars with the JB replacement ratios at 28 of curing days are shown in Figure 7.
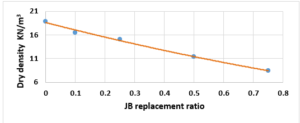
It can be simply detected that increasing the JB ratio decreases the dry density. Reducing density is attributed to certain physical properties, specifically the difference in specific gravity between JB and cement. Additionally, JB exhibits a higher porosity compared to cement, leading to increased volume and reduced overall density.
Investigation of the thermal conductivity (K-value) of the replacement of JB:To illustrate the relationship between thethermal conductivity of cement-JB mixture mortars versus JB replacement ratios, the K-value were determined. JB is categorized by low thermal conductivity against the cement mortar as shown in Figure 8, where the thermal conductivity decreases as the JB ratio increases. In general, as the JB content increased, the k-value decreased, because of its heat-insulating properties, as explained previously. The low K-value indicates that JB can be used as a suitable mortar for high-temperature applications.
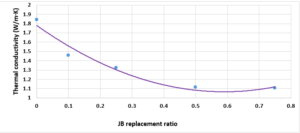
DISCUSSION
Compared with the ASTM C1329 specification, the mortar cement-JB of 10% of JB can be used instead of type M mortar cement (20 MPa) [17]. While the mortar cement-JB of 25% of JB can be used instead of type S mortar (14.5 MPa), which is used in building parts for exterior, at or below grade, and that of 50% of JB may be used instead of type N mortar (6.2 MPa), which is used in building parts for interior non-load-bearing[17]. According to the ASTM specification, the cement-JB mortar of 10% of JB can only be used as type M mortar (0.8 MPa) [17]. While cement-JB mortars with other ratios of JB cannot be used. The initial setting time at 10% of JB is 90 min, which is in accordance with types S and M (not less than 90 min) According to the ASTM C403 specification. As for the final setting time, not more than 1440 min, all of the final setting times are smaller than this value. These setting times are important factors that affect the strength, durability, and workability of cement. For this reason, 10% of JB can be considered a suitable additive for cement within the standard limit to accomplish the best outcomes in building projects. The maximum expansion ratio at 75% reached 24 mm compared to 0% of JB, which was 16 mm. As for mortar with 10% of JB was 18 mm (only 2 mm increasing related to 0%). Thisconfirms that the JB does not display any considerable consequent expansion. If the expansion value is more than 10 mm, the JB-cement mortar is unreliable as described in ASTM specifications [17]. Consequently, the addition of JB had a positive outcome in the avoidance of the shrinkage property of cement that may lead to the formation of plaster cracks or deficiencies. A higher cement fineness provides very good quality, where smaller particles react faster than bigger particles. A cement particle that has a size of 10µm needs around 30 days to achieve the entire reaction, whereas a particle with a size of 1µm does not need more than 24 hours to achieve the entire reaction [18]. All of the water absorption ratios are less than 70%, which satisfies the conditions of ASTM specifications [17]. Cement mortar needs more amount of water (before and after applying, which causes the site to get very dirty) than the JB containing mortars, which means more time during the curing period in contrast with JB mortars that dry quickly and do not require any more treatment water. Mixing JB with cement at different proportions of 10%, 25%, 50%, and 75% of the cement weight does not considerably modify the dry density of the control cement mortar, which was about 18.9 KN/m3 and for the cement-JB mortar of 10%, 25% of JB was 16.5 and 15.1 KN/m3 respectively, and the reduction ratio relative to the control cement mortar was 14.5 %, 20% respectively. The two preceding types of cement-JB mortars are considered to be heavy-weight (greater than 15 KN/m3) [19]. Consequently, the addition of JB had a positive outcome in the avoidance of substantial volume changes, which lead to cracks in the plaster, or adherence deficiency to the wall support. The quantity of energy needed to cool and heat a building is reliant on the k-value [20]. The materials with a lower value of thermal conductivity have greater capability to restrain heat transmission. There are many factors affecting k-value such as mixture kind, percentage of fine aggregate, total volume of aggregate percentage, ratio of (W/C), humidity and temperature conditions, and additive types (fly ash silica fume, blast furnace slag) [20]. The results show that the thermal conductivity of cement-JB mortars increases as the ratio of JB of it gets larger. Thus such mortars are suitable for high-temperature applications and that is why the ancient residents of Deir EZZOR, whose weather is considered to be very hot, have been using the mortar of pure JB to cover their homes.
CONCLUSIONS
This paper presents the potential of combining JB and cement in the process of production of cement-JB mortars that may be used in the construction sector. Although the obtained compressive and flexural strength values were lower than those of control cement mortar, there is an encouraging outcome of the usage of JB in cement-JB mixture mortars, as the compressive strength at 10% of JB, meets the standard specification for type M cement mortar. Whereas the cement-JB mortar at 25% of JB may be used instead of type S mortar. The addition of JB to the cement mortars decreases the thermal conductivity, which gives good thermal properties and ensures energy saving. Cement mortar is prone to cracking, most cracks are caused by shrinkage, which is very common, while JB-added mortar has high elasticity and is less prone to cracking, All of the JB ratios do not show any significant expansion values, where the maximum ratio of 8 mm compared to 0% of JB. In addition, the JB is hydrophobic which results in the moisture not remaining on the interior walls for a long time which will cause no formation of mould and mildew on these walls and prevent them of being slippery. JB-cement mortar dries quickly, which has a 90 min initial setting time at 10% of JB, so it does not require any additional treatment water as the cement mortar which needs a great amount of it (before and after applying). The study also stated that increasing the JB ratio decreases the dry density; the reduction ratio was 14.5 %, 20% at 10%, 25% of JB, respectively. More particularly, it has been probable to confirm that the cement-JB mixture mortars with 10% or 25% of JB accomplish worthy properties, although these mortars do not meet the standards achieved by control cement mortars. On the other hand, the cement-JB mixture mortars may be used in rehabilitation works and rural buildings as a sustainable solution. Also, they can be used, as they were locally used, as interior coverage of walls and roofs in high-temperature cities like Deir EZZOR to reduce their thermal conductivity and make houses more thermally comfortable.
References :- Zengqin Shi, Shuangshuang Xu, Xiaodong Li. Study of mortar layer property of superhydrophobic metakaolin based cement mortar. Journal of Building Engineering. 2022 January; 45: 103578. https://doi.org/10.1016/j.jobe.2021.103578.
- Columbu, S.; Depalmas, A.; Brodu, G.; Gallello, G.; Fancello, D. Mining Exploration, Raw Materials and Production Technologies of Mortars in the Different Civilization Periods in Menorca Island (Spain). Minerals. 2022 February; 12 (2): 218. https://doi.org/10.3390/min12020218.
- Scrivener, K. L., John, V. M. & Gartner, E. M. Eco-efficient cements: Potential economically viable solutions for a low-CO2 cement-based materials industry. Cement and Concrete Research. 2018 December; 114: 2–26. https://doi.org/10.1016/j.cemconres.2018.03.015.
- Miller, S. A., Horvath, A. & Monteiro, P. J. M. Impacts of booming concrete production on water resources worldwide. Nature Sustainability. 2018 January; 1: 69–76.
- Hussein, T.; Kurda, R.; Mosaberpanah, M.; Alyousef, R. A Review of the Combined Effect of Fibers and Nano Materials on the Technical Performance of Mortar and Concrete. Sustainability. 2022 March; 14 (6): 3464. https://doi.org/10.3390/su14063464.
- Miller, S. A. & Moore, F. C. Climate and health damages from global concrete production. Nature Climate Change. 2020 March; 10: 439–443. doi: 10.1038/s41558-020-0733-0.
- Pedreño-Rojas, M.A. & Fořt, Jan & Černý, Robert & Liñán, Carmen. Life cycle assessment of natural and recycled gypsum production in the Spanish context. Journal of Cleaner Production. 2020 April; 253:120056.doi:10.1016/j.jclepro.2020.120056.
- Mercedes del Río-Merino, Alejandra Vidales-Barriguete, Carolina Pi˜na-Ramírez. A review of the research about gypsum mortars with waste aggregates. Journal of Building Engineering. 2022 January;45:103338.https://doi.org/10.1016/j.jobe.2021.103338.
- Ranesi, A.; Faria, P.; Correia,R.; Freire, M.T.; Veiga, R.; Gonçalves, M. Gypsum Mortars with Acacia dealbata Biomass Waste Additions: Effect of Different Fractions and Contents. Buildings. 2022 March; 12 (3): 339. https://doi.org/10.3390/
- Karim Ali Naman, Johansson P¨ar, Sasic Kalagasidis Angela. Knowledge gaps regarding the hygrothermal and long-term performance of aerogel-based coating mortars. Construction and Building Materials. 2022 January; 314 (Part A, 3): 125602. https://doi.org/10.1016/j.conbuildmat.2021.125602.
- Sarcinella, A.; de Aguiar, J.L.B.; Frigione, M. Physical Properties of Eco-Sustainable Form-Stable Phase Change Materials Included in Mortars Suitable for Buildings Located in Different Continental Regions. Materials. 2022 March; 15 (7): 2497. https://doi.org/10.3390/ma15072497.
- Daniel Ferr´andez, Engerst Yedra, Evangelina Atanes-S´anchez, Carlos Mor´on a. Arduino based monitoring system for materials used in façade rehabilitation – Experimental study with lime mortars. Case Studies in Construction Materials. 2022 June; 16: e00985. https://doi.org/10.1016/j.cscm.2022.e00985.
- ; Laím, L.; Santiago A.; Durães, L.; Shahbazian, A. Development of Passive Fire Protection Mortars. Appl. Sci. 2022 February; 12 (4), 2093. https://doi.org/10.3390/ app12042093.
- Habert, G., Miller, S.A., John, V.M. et al. Environmental impacts and decarbonization strategies in the cement and concrete industries. nature reviews earth & environment. 2020 September; 1: 559–573. https://doi.org/10.1038/s43017-020-0093-3.
- B. Singh, B. Middendorf. Calcium sulphate hemihydrate hydration leading to gypsum crystallization. Progress in Crystal Growth and Characterization of Materials. 2007 March; 53 (1): 57-77. https://doi.org/10.1016/j.pcrysgrow.2007.01.002
- J L Ricci, M J Weiner, S Mamidwar, H Alexander. 14 – Calcium sulfate.Editor(s): Tadashi Kokubo, In Woodhead Publishing Series in Biomaterials, Bioceramics and their Clinical Applications, Woodhead Publishing. Available online, 2014 March; Pages 302-325, https://doi.org/10.1533/9781845694227.2.302.
- Mortar cement types N, S, and M [internet]. CEMEX building the future, U.S. operations headquarters; Available from: https://www.cemexusa.com/documents/27329108/45560536/cemex-mortar-cement-data-sheet.pdf/462a0223-80a6-683e-b984-a25dcce696af.
- Bhushan Mahajan. Cement of Fineness: Definition, importance, and how to test it [internet]. Available from: https://civiconcepts.com/blog/fineness-of-cement.
- Duggal. Building materials, third revised edition. motilal nehru institute of technologym Allahabad (U.P.). 2018.
- Shafigh, P.; Asadi, I.; Akhiani, A.R.; Mahyuddin, N.B.; Hashemi, M. Thermal properties of cement mortar with different mix proportions. Materiales de Construcción. 2020 September; 70 (339): e224. https://doi.org/10.3989/mc.2020.09219.
The Authors declare that they have no competing interests.
(ISSN - Online)
2959-8591